PRINTING
RECOMMENDED TEST PROCEDURES
Printing Temperature
Finding the optimum temperature depends on your model and its purpose. So when it comes to finding the perfect printing temperature, its worth running a test procedure first to match your print settings to the desired results. These test procedures usually take a couple of hours to print, but the knowledge gained is invaluable when creating your printing profile.
The material manufacturers recommendation is the best place to start, however this is often displayed as a temperature range rather than an exact figure. This is due to the fact that every 3D printer will achieve slightly different printing temperatures and the material itself will extrude through a temperature range of roughly 20°C. The higher the temperature, the stronger the bond between layers and therefore the stronger the final printed part will be. However too high, and you will run into printing issues such as sagging, rough surface finish and dimensional inaccuracy. Towards the lower end of the temperature range, you will notice a better surface finish but the part strength won’t be optimised. Finding the ideal temperature greatly depends on the geometry of the model that you are planning to print. For example a finely detailed model incurring multiple retractions per layer and thin walled sections may favour a temperature towards the lower end. Whereas a less complex geometry such as a solid jig or fixture designed for toughness would be better suited with a higher printing temperature. This model is a good way of finding the correct printing temperature. The model is split into seven sections, when slicing your model, set the temperature to change at each section using increments of 5°C. You can then analyse the print afterwards and decide the best temperature for your print.
Extrusion Multiplier
The extrusion multiplier is a variable that adjusts how much material is extruded in relation to the speed of the hot end/nozzle diameter. The extrusion multiplier will effect the dimensional accuracy of your printed parts and can adversely effect the strength and interlayer adhesion if it is set too low. Too high and the accuracy of the print will be compromised as too much plastic will be extruded, usually multiplying the problem with every layer, until catastrophic failure. The extrusion multiplier can vary a large amount from printer to printer and doesn’t always scale well when interchanging nozzle diameters. The extrusion multiplier can also be effected by a number of external factors linked to printer maintenance. Such factors could be; the state/age of the nozzle, as plastic is heated and passed through the nozzle, over time a layer of carbonised plastic will build up on the inside of the nozzle restricting extrusion. Another factor could be a clogged extruder gear, or the tightness of the idler wheel gripping the filament. While these problems are rare, its worth mentioning as they will need to be considered at some point.
The viscosity of molten polycarbonate is a little higher than other 3D printing materials, so a good place to start is 1.00 or 100% extrusion and test the results and likely increase the multiplier. We recommend printing this calibration cube to test your extrusion multiplier, it is a quick and effective method that will quick iteration. Once printed, measure the cube with a set of digital calipers and pay special attention to the corners, the debossed text and the top surface. The cube should measure square at 20mm, the corners should be well defined and the top surface should have no gaps.
Retraction
The retraction test procedure will save you plenty of time in post processing once it has been dialled in. Poor retraction can lead to blobs on the surface of the printed model, strings between gaps and an uneven seem line. Most of these problems are aesthetic and will have little effect on the strength of you part, unless they are wildly untuned.
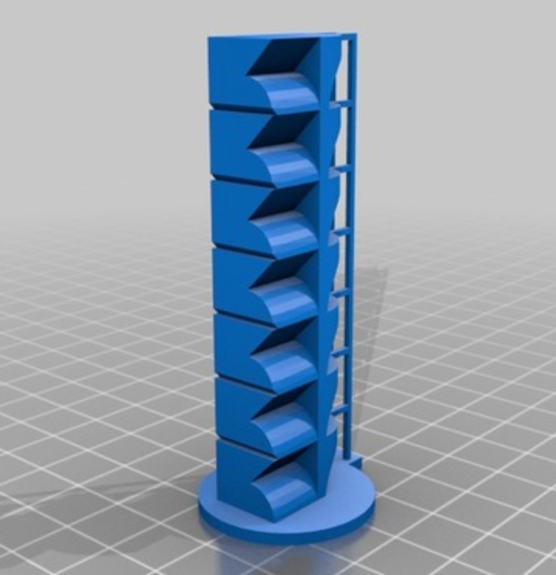

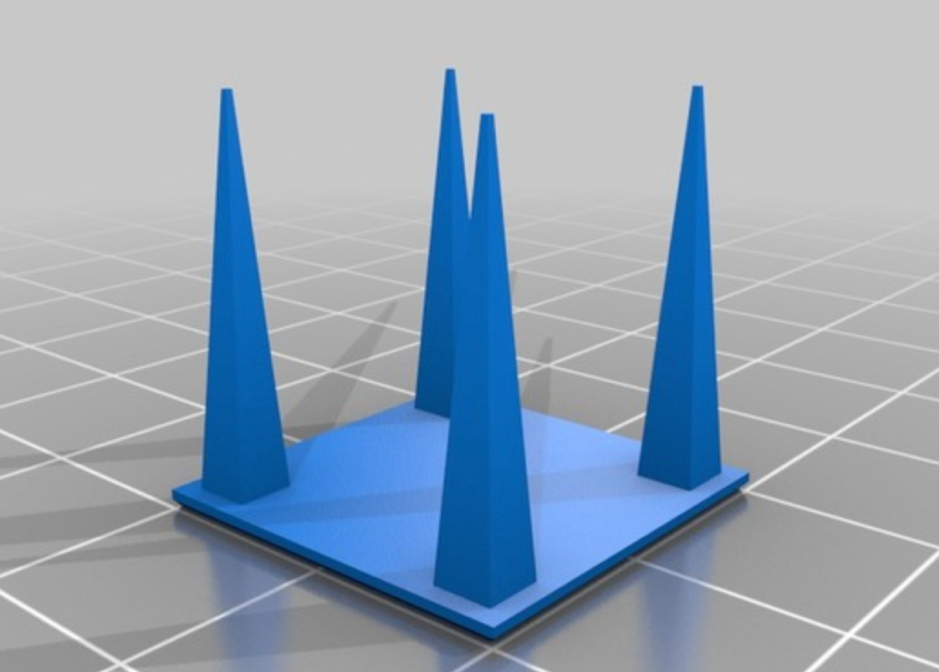